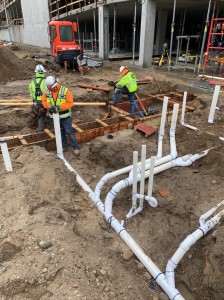
Members of our team laying groundwork plumbing, 2020
In our nearly fifty years in business, we’ve grown to provide plumbing in Utah, Colorado & Idaho, and HVAC in Utah and Colorado. Our company has grown and taken on significant projects as a team. We’ve moved from residential projects to large-scale builds, multi-family units, and commercial buildings. It’s been a lot of work.
To guide this growth, we’ve embraced the management strategy ‘The Theory of Constraints.’ This theory was proposed in the 1984 book, The Goal by Israeli business management expert Dr. Eliyahu M. Goldratt. A variety of industries has adopted his theory. Here’s a quick overview of it.
The Theory of Constraints or TOC management theory recognizes that there must be problems to overcome before every goal can be achieved. Using this theory, organizations must plan for each problem or ‘constraint’ that stands in the way of achieving the end goal. When one constraint is dealt with, the next constraint becomes the focus.
This method of management organization is especially useful in our line of work. We often start from the ground up, laying pipe, creating or following design plans, and then continuing our work through the finished project. We work with various partners and contractors, and all the moving pieces must come together to create the finished design. Everyone must work together to achieve the end goal and solve each constraint together to improve everyone’s process. One of the TOC theory tenants is the interconnectedness and links between each step of the process.
There are five basic steps to the TOC management theory. To demonstrate how these steps can be used, we’ll present the example of a new worker’s problem on an assembly line.
- Identify: Find the part of the system that is weak and causing problems. Example: Productivity targets are down because of system bottlenecks at the new employee’s station.
- Exploit: Get as much as you can out of the weak area without improving it. Example: Identity what target quota the new employee can meet on their own.
- Subordinate: Adjust the other system processes to the level of the weak area. Example: Reduce the assembly line’s overall speed and productivity targets to help the new employee catch up.
- Elevate: Improve the constraint or eliminate the problem if steps 2 or 3 are not successful. Example: If the new employee speeds up, the issue is solved. If the new employee does not, take the employee out of the line.
- Inertia: Repeat the process with the next constraint, but be careful not to let the problem repeat itself. Example: Repeat this process with new employees to help them learn their job and role efficiently.
The example of the new assembly line worker struggling to keep up is a simplistic view of the TOC management theory, but it illustrates the point. The end goal is to meet the output quota, but that goal can’t be achieved if something or someone is getting in the way. By identifying the problem and working together to fix the issue, the final result is achieved.
We’ve practiced this management theory for many years now for much more complex goals and processes. It’s served us well each time and helped us develop a mentality for excellence and strong teamwork. Give it a try in your business and see what it can do!